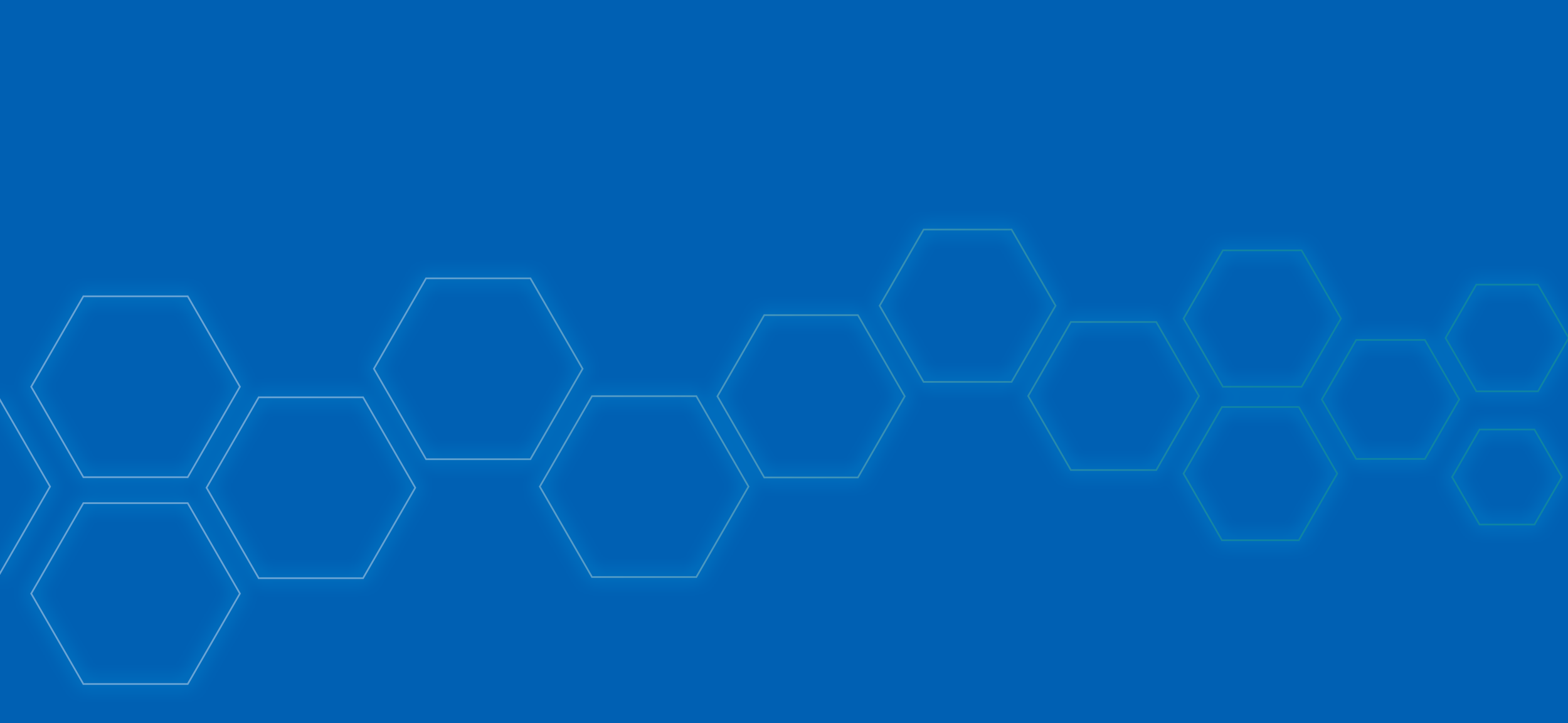
Hoppers
Hoppers are built for bulk part storage. There are commonly two types of hopper drivers, vibratory and conveyor. This is what actually moves the parts into the feed system from the bulk storage. The hopper bin, stand, and mounting can be customized to fit your needs and space requirements. They are tied to the feed system with a sensor shutting the flow of parts on and off as needed.
Hoppers come in a lot of different shapes and sizes, and have some different options available. The hopper tray is the interface between the storage bin and the feed system. On traditional hoppers, the storage bin sits above the tray, which sits above the feeder. This pushes loads heights up and can cause some issues. The answer to this is to change from a traditional hopper to an incline conveyor hopper. This allows the storage bin to sit at ergonomically safe heights. One option available on hoppers is a low level alert light, that will notify the operator that the part level is running low and it’s time to refill the hopper.
Hoppers are beneficial in a couple of ways. First, they extend the runtime between filling cycles. Second, they regulate the amount of parts in a the feed system. Some feed systems can work well with a lot of different levels of parts in the bowl, but most work well with a small range, which can be difficult to maintain by hand. The hopper does this well and allows the system to work at it’s most efficient setting.
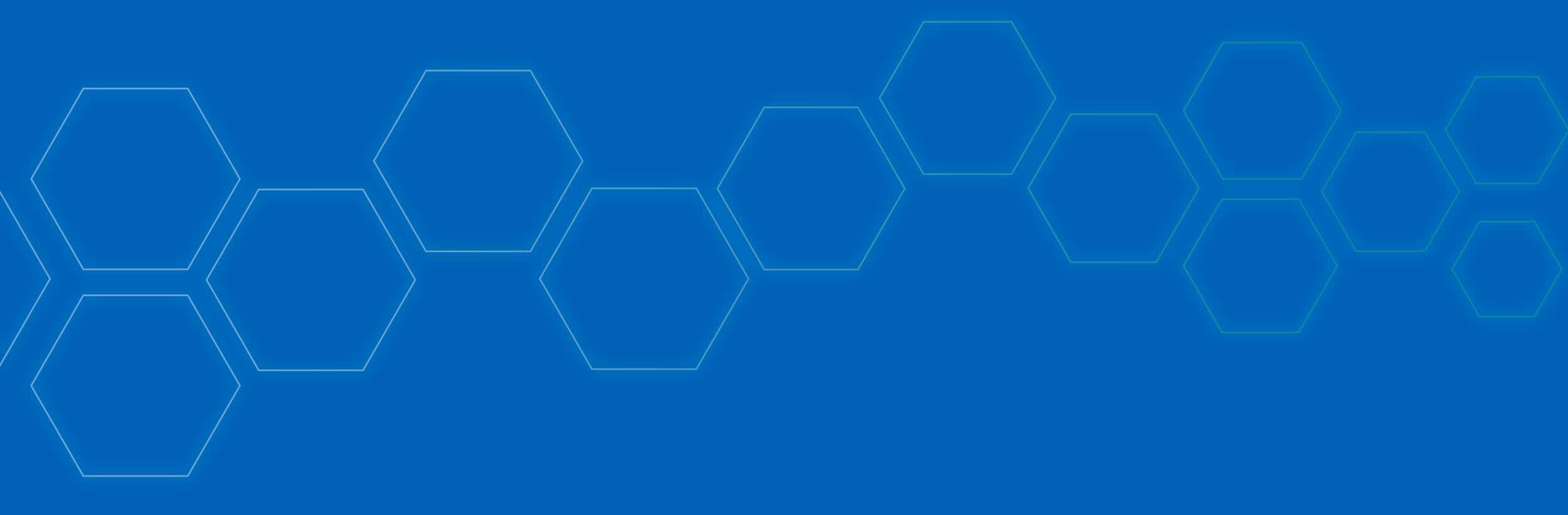
Have questions about Hoppers?
Email us and we will be happy to help answer any questions you might have!